How to Save Energy in All Aspects of Feed Pellet Mill Processing
Energy-saving is a point that every feed processing factory is very concerned about. In the daily production process, how to reduce energy consumption and increase production to a greater extent, Henan Herm Machinery recommends that you need to do the following.
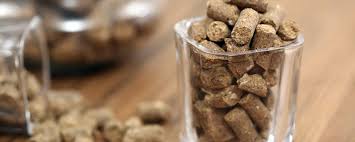
One, How the power transmission system save energy consumption?
Poultry feed equipment and equipment all transmit power through transmission devices such as bearings, reducers, and transmission belts. Therefore, we must first ensure the normal operation and lubrication of the transmission devices to reduce the loss of power in the transmission process and achieve energy-saving effects.
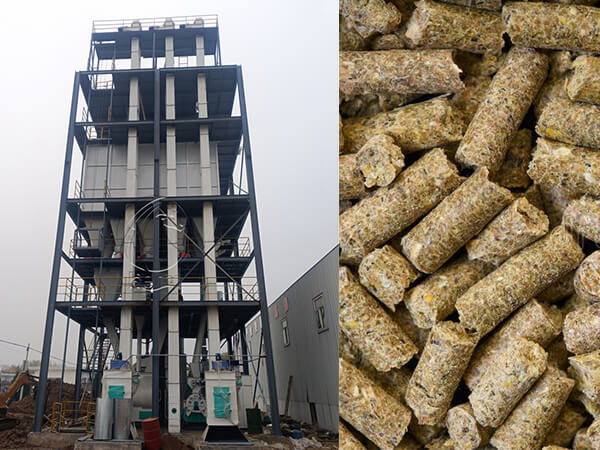
1. Select the appropriate type of lubricant and the amount used to ensure that the feed equipment has a good working environment and state;
2. Keep the drive belt at a proper tension level, replace the worn drive belt, and use pulleys and other devices that match the drive belt;
3. Avoid the vibration of the transmission equipment caused by the loose chain, and keep the chain at an appropriate tightness;
4. Keep the transmission device clean and free of dirt and waste accumulation to avoid local excessive heat collection. Allow free flow of air around the gear reducer;
5. When the equipment must work at more than one speed, use an AC variable frequency drive instead of a mechanical and adjustable belt drive;
6. Minimize or avoid the use of pneumatic conveying systems as much as possible.
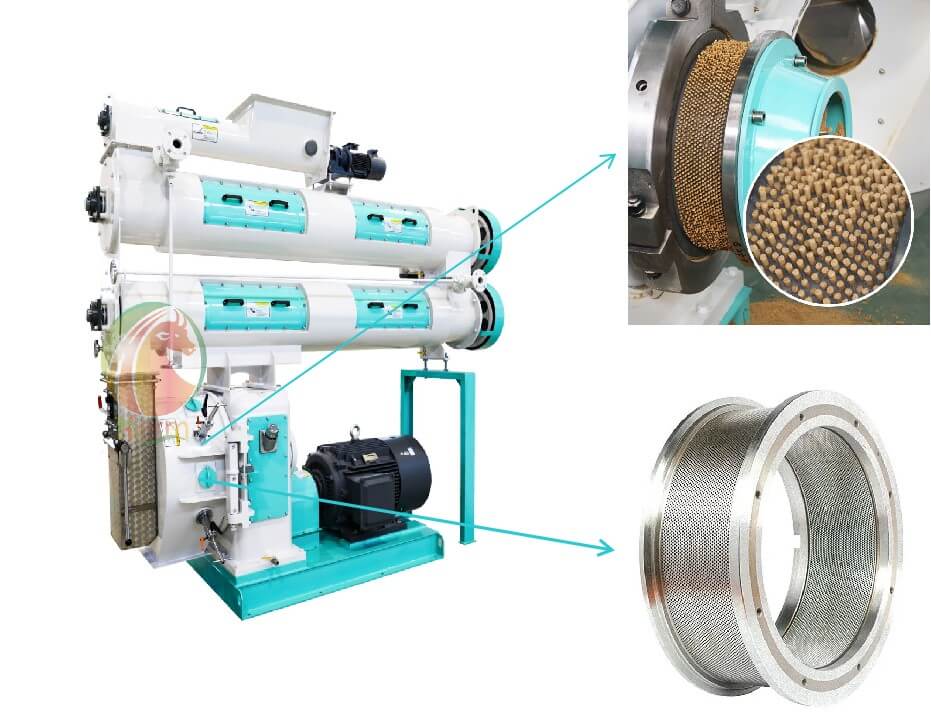
Two, How to save energy in the feed raw materials crushing process?
1. Reverse the hammer in time or replace the hammer and cloth bag to improve the crushing efficiency;
2. Keep the negative pressure of the air assist system in good condition to increase the output. After the pulse fan stops, the pulse bag will be cleaned after a delay to ensure that the bag is clean, which can improve the service time of the bag and improve the efficiency of the fan;
3. Use the variable speed feeder to feed the material evenly and keep the load of the feed crusher machine constant;
4. In the micro-grinding operation, the hard-to-grind and easy-to-grind raw materials are mixed for micro-grinding, which can improve the micro-grinding efficiency;
5. Add grading equipment after primary pulverization and fine pulverization to reduce the excessive crushing of raw materials.
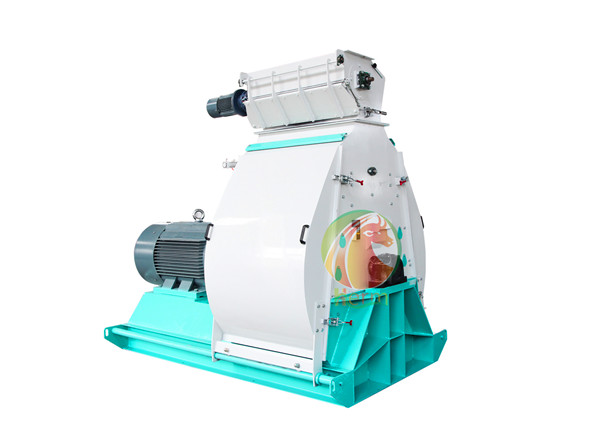
Three, How to save energy in mixing and batching?
1. Improve the operation skills and coordination level of the central control personnel. When the operator goes to work and receives the task, according to the production task list, the number of raw materials in stock in the batching warehouse and the warehouse capacity, the type, sequence, and quantity of the feeding personnel are determined to ensure that the mixer works continuously and will not stop production due to the interruption of a certain raw material; Reasonable feeding will ensure that the feed crusher machine starts less frequently and has the shortest idle running time within a certain period of time; when granules and concentrated materials are produced at the same time, determining the appropriate switching time is an important guarantee to maintain the continuous production of the pellet feed making machine and the feed mixer machine. If the central control personnel are not skilled in the operation and have low coordination ability, the production process will inevitably encounter problems such as poor production or shutdown due to material failure. Therefore, improving the operation and coordination level of the central control personnel is an important aspect of improving production efficiency.
2. Use the variable frequency variable speed controller for the screw feeder to keep the feeder motor load stable and efficient.
3. The design of the silo and scale bucket should ensure that the material is completely discharged by self-flow, without using vibration discharge or mechanical discharge, or a mechanical discharge device.
4. Correctly set the batching and mixing cycle, reasonably arrange manual feeding and liquid-adding operations, and improve the efficiency of batching and mixing operations.
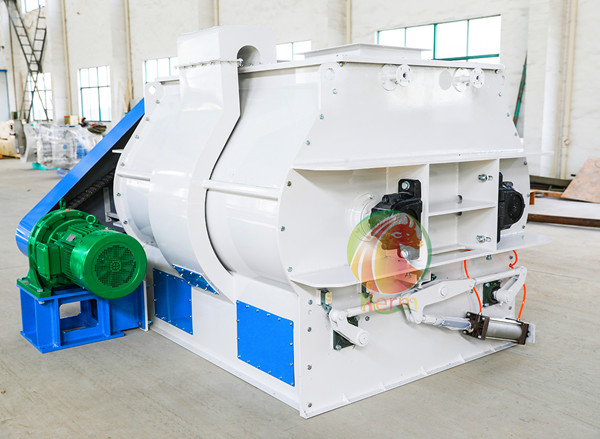
Fourth, how to save energy in the feed pelleting process?
1. When purchasing the ring die of the feed pelletizer and the screen of the feed crusher machine, the opening rate should be increased as much as possible under the premise of ensuring the strength, so as to improve production efficiency and reduce power consumption.
2. Reasonably control the output, reasonably adjust the die roll gap, improve the feed pelletizing efficiency, and prolong the life of the ring die and the pressing roll.
3. Use the ring mold repairing machine to repair the ring mold in time to improve the granulation production efficiency.
4. Adjust or replace the blades of the conditioner of the feed pellet machine, and add a stirring rod to the conditioner to improve the conditioning effect and increase production efficiency.
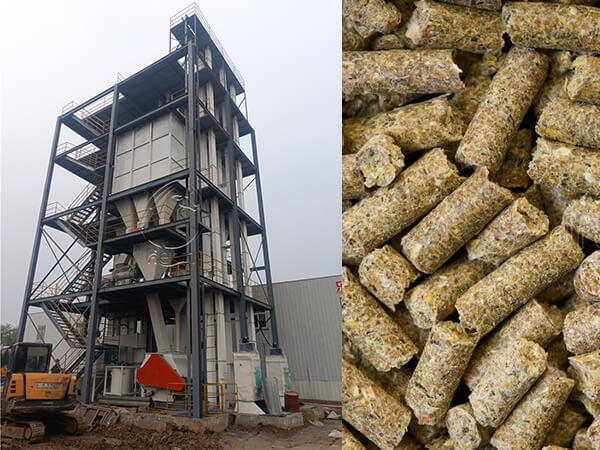
Henan Herm Machinery Co., Ltd was established in 2010 and has been devoted to the research and development of Feed Mill Machinery ever since. With more than 10 years of experience, Herm® has become a leading manufacturer and supplier of animal feed machines and complete animal feed production lines, cattle feed plants, poultry feed plants, animal feed pellet production lines, etc. It always endeavored to improve the quality of products and aims to meet the new requirements of the international market.
If You Are Ready to Start a Feed Pellet Plant Business, please contact us for the feed mill machine. We Can Provide Professional Design and Comprehensive Guidance According to Your Needs. Get in touch with us now!
Welcome Contact Us!
Henan Herm Machinery Co., Ltd
Email: info@hermmachinery.com
Whatsapp: 0086 18037508651