Factors Influencing the Production Benefits of Feed Pellet Machines
Due to challenges in process design and operational technology, the feed factory faced issues with the quality and output of its finished products. The particles exhibited uneven surfaces, high powder content, brittleness, and inconsistency. A comprehensive practical analysis revealed several critical factors influencing granulation efficiency:
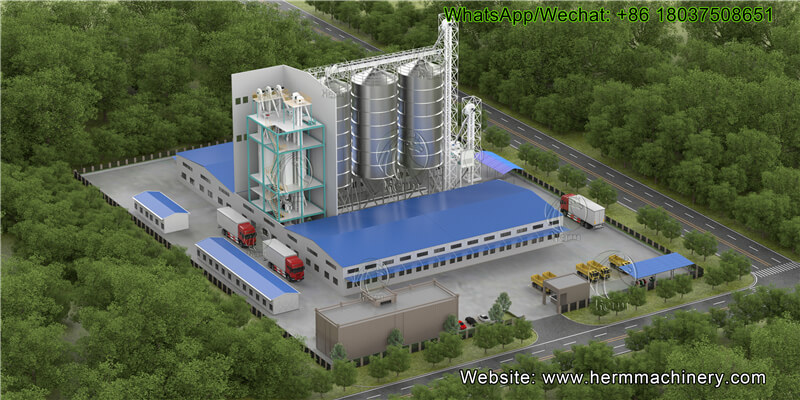
Raw Materials:
Starch Content: High starch content facilitates gelatinization, which, when combined with proper conditioning, creates a conducive, viscous state for effective molding.
Crude Fiber: Elevated crude fiber increases friction in the ring die. The addition of a specific amount of grease aids material passage through the die hole and enhances the surface finish of the final product.
Crushing Diameter: Optimal crushing diameters vary based on raw materials. For instance, using a 2.5-3mm sieve plate is recommended for crushed corn in livestock and poultry feed.
Formulas and Mixing Time: Different raw materials necessitate distinct formulas and mixing times. Achieving a mixing coefficient of around 5% before granulation is essential for uniformity.
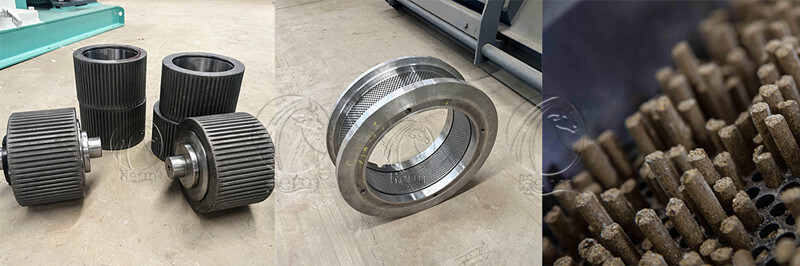
Feed Control:
Comprehensive Monitoring: During periods of reduced production efficiency, addressing pelleting issues alone is insufficient. Comprehensive monitoring of incoming material control is crucial.
Stabilizing Feed Flow: Recognizing and rectifying causes of feed flow instability ensures a continuous and even operation of the poultry pellet feed machine at full load.
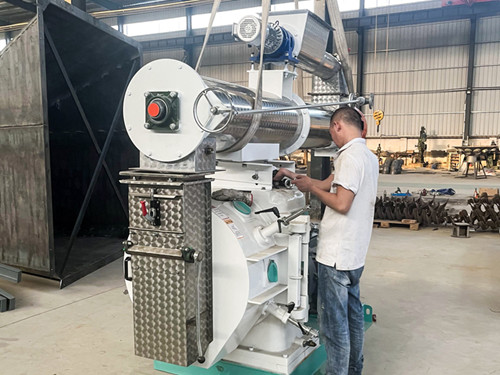
Production Operation:
Precise Adjustments: Fine-tuning each part of the poultry feed pellet machine, including the die and pressure roller (controlled at 0.05~0.30 mm), prevents issues such as excessive noise and ensures optimal material granulation.
Gap Control: Maintaining a controlled gap of 2-3 mm between the upper edge curve of the scraper and the die and die cover is critical for smooth pellet feed machine operation.
Start-Up Observations: Careful observation during start-up helps identify irregularities in particle discharge. Preventing the introduction of contaminants into the die contributes to a more efficient granulation process.
Ring Die:
Factors Influencing Material Ejection: Factors like the friction coefficient between the material and the die wall, moisture content, particle size, temperature, plasticity, and compressibility influence the smooth ejection of material.
Compression Ratio: Recommending a compression ratio of 1:8 to 1:13 for the ring die diameter ensures a balanced trade-off between efficiency, surface smoothness, tightness, and output.
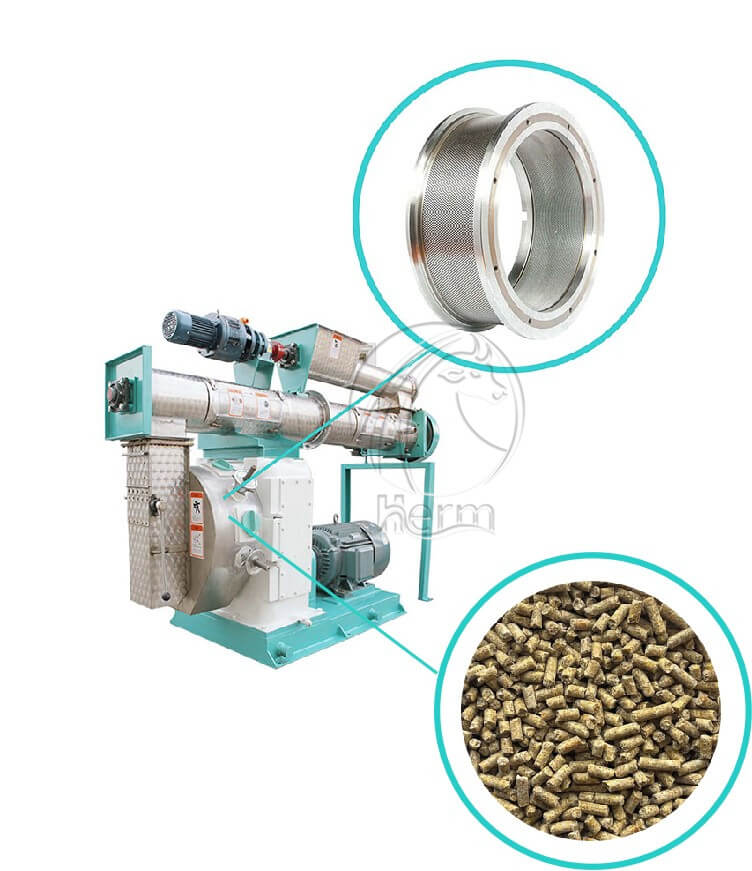
Conditioning Factors:
Blade Wear Impact: Worn conditioner blades negatively impact material conditioning, affecting particle output and steam absorption.
Material Softening: Proper softening of conditioner material is crucial for achieving the desired pulverization rate and output.
Temperature Control: Specific temperature recommendations, like 70~88°C for livestock and poultry feed, optimize conditioning effects.
Steam Factor:
Steam Conveyance Challenges: Saturated steam entry during conveying results in energy loss and condensed water formation, negatively affecting conditioning.
Condensed Water Management: Discharging condensed water before conditioning and converting it into low-pressure dry hot steam through a pressure-reducing valve enhances conditioning effects.
Pressure and Temperature Control: Maintaining steam pressure above 0.2 MPa and a temperature not lower than 120 ℃ post-decompression ensures an optimized conditioning process.
By addressing these factors systematically, the feed factory can optimize the performance of the feed pellet machine, improving product quality and increasing overall output.
Henan Herm Machinery Co., Ltd was established in 2010 and has been devoted to the research and development of Feed Mill Machinery ever since. With more than 10 years of experience, Herm® has become a leading manufacturer and supplier of animal feed machines and complete animal feed production lines, cattle feed plants, poultry feed plants, animal feed pellet production lines, etc. It always endeavored to improve the quality of products and aims to meet the new requirements of the international market.
If You Are Ready to Start a Feed Pellet Plant Business, please contact us for the feed mill machine. We Can Provide Professional Design and Comprehensive Guidance According to Your Needs. Get in touch with us now!
Welcome Contact Us!
Henan Herm Machinery Co., Ltd
Email: info@hermmachinery.com
Phone/Whatsapp: 0086-18037508651