Essential Steps for Making High-Quality Animal Feed Pellets
Comprehensive Guide to Animal Feed Pellet-Making Machines
Animal feed pellet-making machines are essential for farmers and feed processing factories. They enable the production of various pellet sizes tailored to specific livestock needs, such as pork and chicken feed. Our versatile machines can efficiently produce different pellet sizes, ensuring you receive the appropriate die for your requirements. Whether for large-scale or small-scale production, our equipment is designed to meet your needs effectively.
Make a Quick Inquiry Now !Step 1: Selecting the Right Pork Feed Material
Choosing the appropriate feed material is crucial for maximizing animal health and production efficiency. Energy feeds contain less than 18% crude fiber and less than 20% crude protein in dry matter. Common energy sources include grains, bran, starch, roots, tubers, and by-products, providing more than 10.46 MJ of energy per kilogram.
Protein feeds include ingredients such as beans, cakes, and fish meal, characterized by a natural moisture content below 45%, a crude fiber content lower than 18%, and a crude protein level of 20% or higher in dry matter.
Additionally, mineral additive premixes consist of naturally occurring minerals and industrially synthesized compounds, delivering essential macro and micro elements necessary for livestock health. Each factory typically employs a dedicated formulation expert to customize feed based on specific animal needs.
Step 2: Crushing the Material into Powder
Crushing raw feed materials is a vital process in feed production. This step increases the surface area of raw material particles, enhancing the solubility of nutrients in animal digestive fluids and improving overall digestibility. The size of the powder significantly impacts subsequent processes, such as granulation, and the quality of the final product. It also directly affects production costs. The important equipment is the water drop feed hammer mill machine.
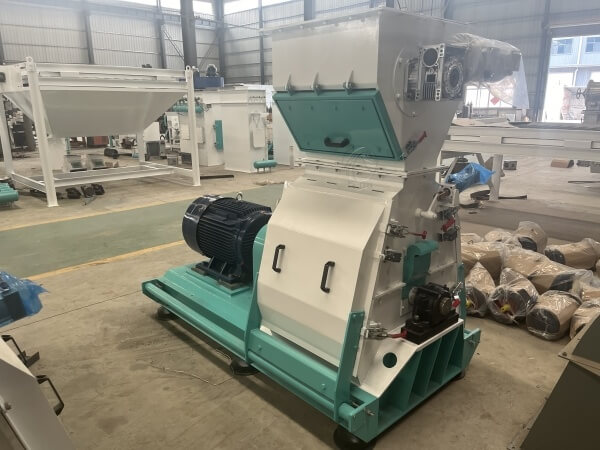
In the production of powdered compound feeds, crushing consumes about 50% to 70% of the total energy used. A smaller particle size promotes better digestion and nutrient absorption in animals and facilitates granulation, although it also increases energy consumption. With over 200 million tons crushed and processed annually in our country, the feed mill plays a crucial role in ensuring high-quality feed.
To manage dust generated during crushing, our machines can be equipped with pulse dust collectors, ensuring a cleaner working environment.
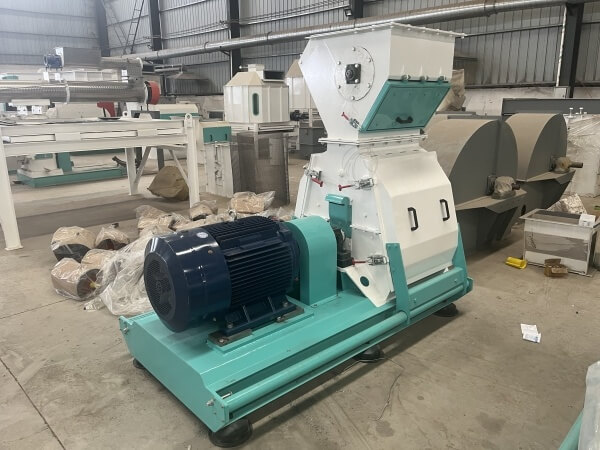
Step 3: Mixing the Powder
Mixing is another critical step, typically conducted using two main types of mixers: horizontal mixers and vertical mixers.
Horizontal feed mixers are widely used in feed processing due to their advantages, including high mixing uniformity, short mixing times, and efficient discharge mechanisms. Common types include stainless steel double-shaft paddle mixers and horizontal ribbon mixers. However, they are generally larger, more expensive, and require regular maintenance compared to vertical mixers.
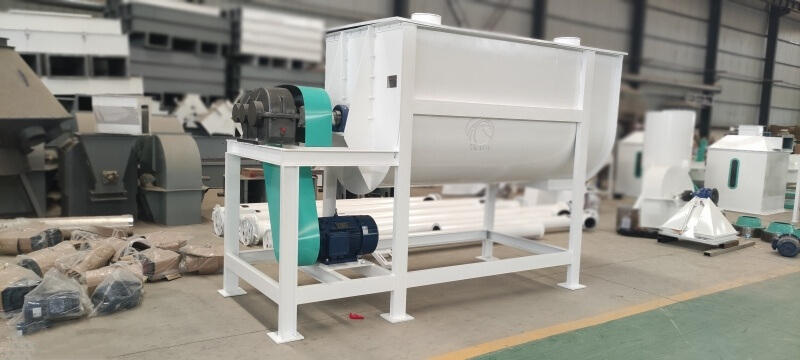
For larger production capacities, horizontal feed mixers are recommended due to their efficiency and stainless steel construction, which enhances durability.
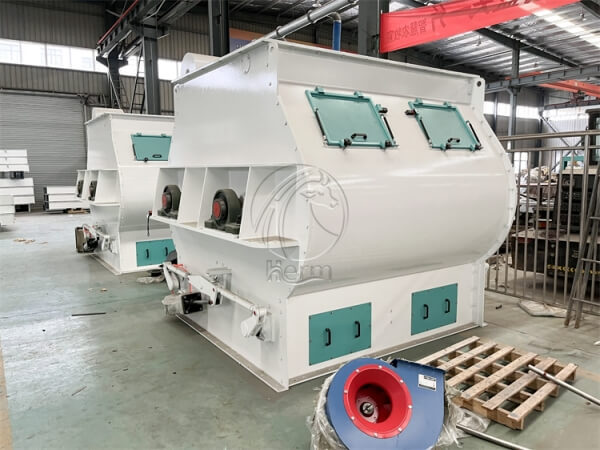
Step 4: Animal Feed Pellet-Making Process
Animal feed pellet machines are categorized into ring die and flat die types.
Flat die pellet machines are suitable for capacities below 1000 kg/h, offering a simple structure and ease of operation.
Ring die pellet machines are ideal for capacities exceeding 1000 kg/h and require steam for operation, necessitating a boiler setup prepared by the buyer.
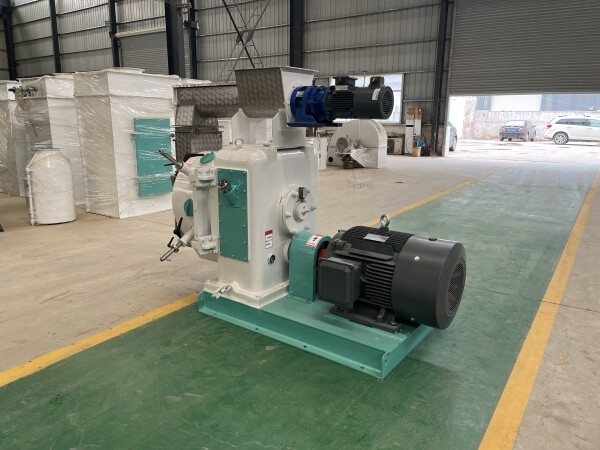
Before operating the ring die machine, it's essential to check the steam pipeline system for effective pressure regulation and moisture removal. The pressure roller's distance from the ring die should be adjusted to 0.1–0.4 mm to prevent friction, which can lead to wear and reduced output.
During startup, gradually introduce feed and steam for 5-10 minutes to reach optimal feeding levels, aiming for 85-95% of the rated current value.
Step 5: Cooling the Pellets
Post-production, cooling is critical. Our feed cooling machines utilize countercurrent cooling principles to ensure that pellets are uniformly cooled. Featuring a unique sliding valve mechanism for smooth material discharge, our cooling solutions maintain pellet temperatures at no more than room temperature plus 3-5°C.
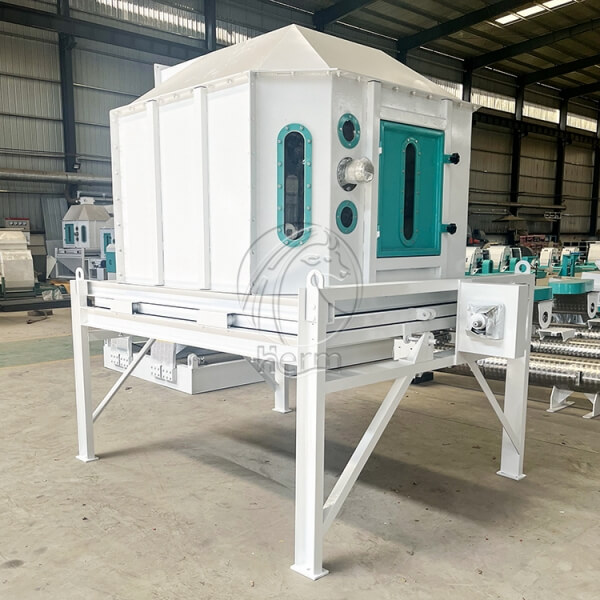
With high output capacity, effective cooling performance, and automated processes, our machines operate quietly and require minimal maintenance, making them an ideal choice for modern feed production facilities.
By following these steps, producers can maximize the efficiency of their animal feed production processes, ensuring high-quality feed that meets the nutritional needs of various livestock.
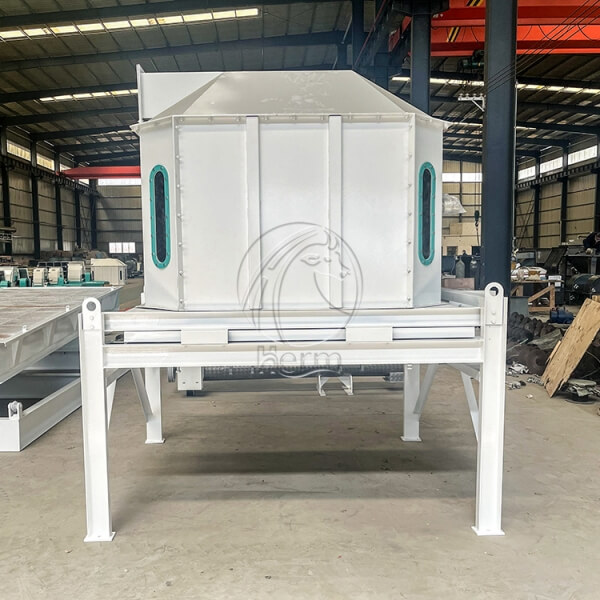
Henan Herm Machinery Co., Ltd was established in 2010 and has been devoted to the research and development of Feed Mill Machinery ever since. With more than 10 years of experience, Herm® has become a leading manufacturer and supplier of animal feed machines and complete animal feed production lines, cattle feed plants, poultry feed plants, animal feed pellet production lines, etc. It always endeavored to improve the quality of products and aims to meet the new requirements of the international market.
If You Are Ready to Start a Feed Pellet Plant Business, please contact us for the feed mill machine. We Can Provide Professional Design and Comprehensive Guidance According to Your Needs. Get in touch with us now!
Welcome Contact Us!
Henan Herm Machinery Co., Ltd
Email: info@hermmachinery.com
Whatsapp: 0086 18037508651