Ways to Ensure Quality Control in the Feed Granulation Process
Requirements for Equipment Before Granulation
Ensuring the quality of the final product starts with thorough inspection and equipment maintenance before production. The following aspects are essential for effective equipment readiness:
Make a Quick Inquiry Now !Magnet Cleaning: Magnets should be cleaned at the beginning of each shift. Failing to do so can allow metal contaminants from the feed to enter the ring die of the pellet feed-making machine, which could disrupt its normal operation and lead to costly repairs.
Monitoring Wear: Regularly monitor the wear on the ring die and pressing roller. Worn pressing rollers can diminish production capacity, while excessive wear on the ring die reduces its effective thickness, negatively impacting pellet quality. Regular assessments can prevent unexpected downtimes.
Lubrication: Ensure that lubricating oil is applied to the pressure roller regularly. Proper lubrication reduces friction, minimizes wear, and ensures the smooth operation of the pressure roller, ultimately enhancing production efficiency.
Cooler Inspection: Inspect the cooler for any material backlog and check the cooling plate's or screen surface's integrity. Blockages or damage in the cooling system can lead to inefficient cooling, affecting the final product's quality.
Crusher Maintenance: The crusher's roller should be examined periodically. If the roller's corrugated teeth are dull, they will reduce crushing capacity and compromise product quality. Regular maintenance ensures optimal performance.
Grading Screen Checks: Each shift, check the grading screen for holes, blockages, and adhesion. The screen surface should be intact to ensure accurate particle classification, critical for achieving uniform product quality.
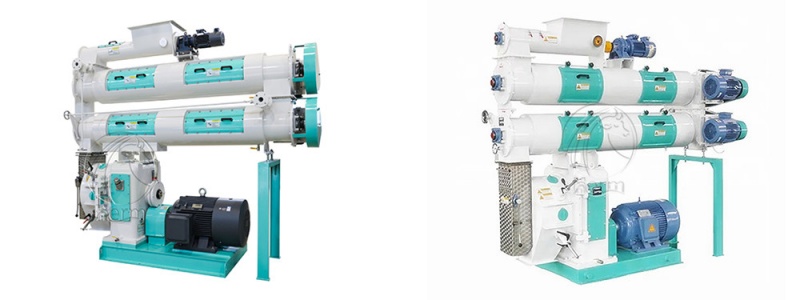
Cutter Evaluation: Assess the condition of the feed pelletizer's cutter. A dull cutter can lead to an increase in feed powder generation, adversely affecting the quality and efficiency of production.
Steam Separator Verification: Ensure the steam separator is functioning properly to maintain high-quality steam entering the conditioner. Poor steam quality can negatively impact both production capacity and pellet quality.
Material Change Procedures: When changing materials, verify that both the buffer storage bin and the finished product storage bin above the animal feed pellet machines are completely emptied. This practice prevents cross-contamination and maintains product integrity.
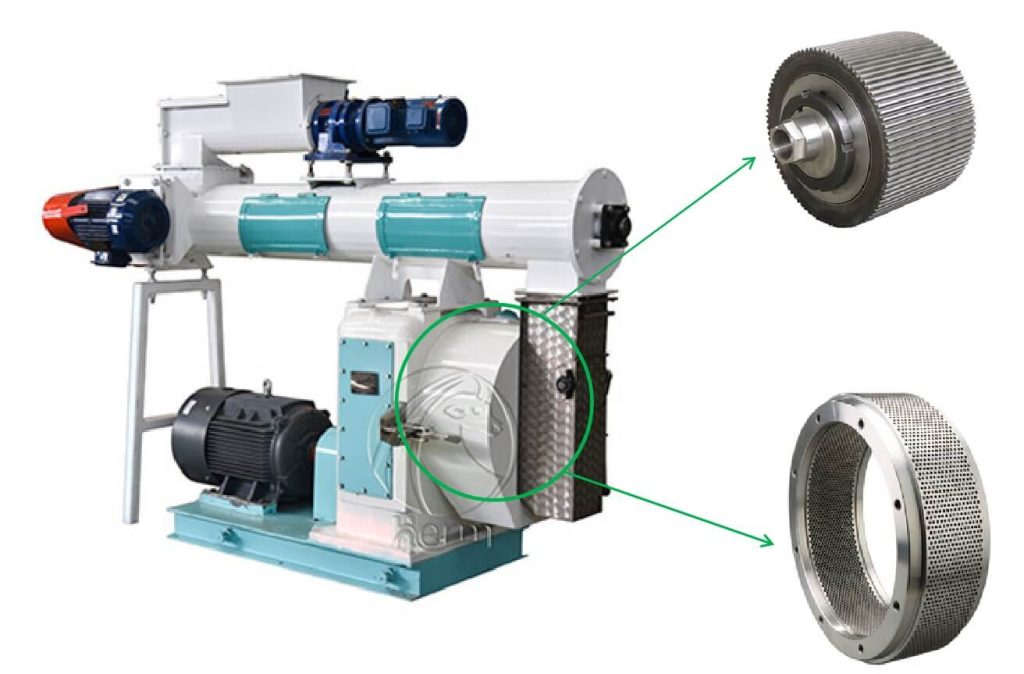
Conditioning and Tempering Technology
The conditioning process is crucial for producing high-quality pig and chicken feed, typically made from sweat corn, which is rich in starch and low in crude fiber. The effectiveness of pelleted feed largely relies on conditioning technology, which employs heat and steam to soften raw materials, enhancing their pelleting performance.
During conditioning, the starch in the feed partially gelatinizes, allowing it to bond effectively and improve the pellet-forming rate. The ideal conditioning time ranges from 10 to 20 seconds. Extending this time can yield multiple benefits:
Increased Starch Gelatinization: This enhances the binding properties of the feed, improving the overall pellet forming rate.
Temperature Management: Higher temperatures during conditioning reduce the presence of harmful microorganisms, contributing to the safety and quality of the feed.
Enhanced Production Efficiency: Proper management of vapor pressure during the conditioning process facilitates quicker dissipation of heat and moisture, further enhancing efficiency.
To achieve optimal conditioning results, the feed moisture should be adjusted to 16-18% and the temperature maintained between 75-85 degrees Celsius, depending on specific operational needs.
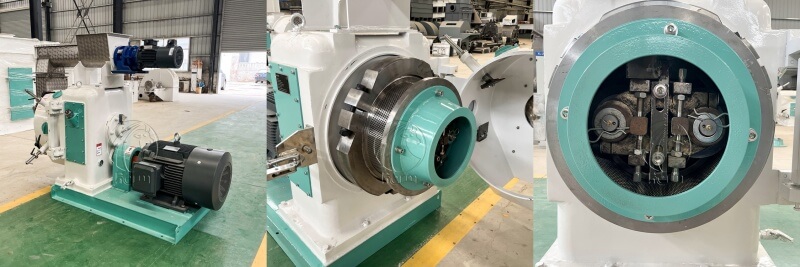
Correct Adjustment of Roller Gaps
Accurate adjustment of the gap between rollers is essential for prolonging the service life of both the ring die and the rollers, while simultaneously improving production efficiency and particle quality. The following adjustment guidelines should be followed:
Pressure Roller Setting: The pressure roller should be adjusted so that, when the ring die rotates at a low speed, it only contacts the high point of the ring die. This minimizes metal contact, reducing wear, and ensuring sufficient pressure is applied during operation.
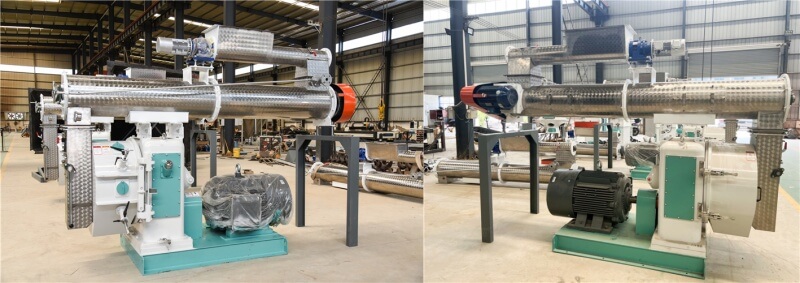
Crushing Particle Size of Granulation Raw Materials
The required particle size for raw material crushing should align with the desired particle size of the final product. Improper particle sizing can lead to inefficiencies:
Too Fine Particle Size: This results in lower processing speeds and decreased productivity.
Too Coarse Particle Size: A larger particle size can lower the pellet forming rate and increase the likelihood of particle damage.
The particle size of the feed can be tailored according to its intended use:
Chicken Feed: Larger particles, typically 15-20 mesh.
Fish and Shrimp Feed: Finer particles, generally in the range of 40-60 mesh.
Specialized Feeds: Certain specialized feeds may require even finer particles, ranging from 80-120 mesh.
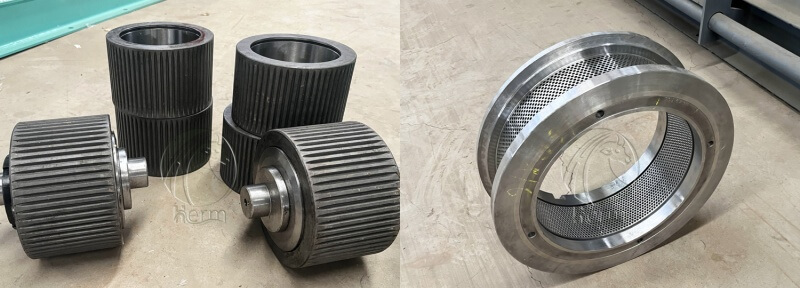
Requirements for Particles
Pellet Forming Rate: To assess the forming rate of pellet feed, use a wire mesh screen with a particle size of less than 20%. For example, if the pellet feed size is 5.00 mm, screening should be done with a 4.00 mm wire mesh. The percentage of oversized particles indicates the forming rate. Livestock and poultry feed should have a pellet forming rate exceeding 95%, while fish and shrimp feed should exceed 98%.
Particle Length: For feed particles with a diameter of less than 4 mm, the length should be 2-5 times the particle size. For those exceeding 4 mm in diameter, the length should be 1.5-3 times the particle size. Proper particle length contributes to improved digestibility and overall feed quality.
By adhering to these comprehensive guidelines, manufacturers can ensure the production of high-quality granulated feed, leading to better animal health and performance.
Henan Herm Machinery Co., Ltd was established in 2010 and has been devoted to the research and development of Feed Mill Machinery ever since. With more than 10 years of experience, Herm® has become a leading manufacturer and supplier of animal feed machines and complete animal feed production lines, cattle feed plants, poultry feed plants, animal feed pellet production lines, etc. It always endeavored to improve the quality of products and aims to meet the new requirements of the international market.
If You Are Ready to Start a Feed Pellet Plant Business, please contact us for the feed mill machine. We Can Provide Professional Design and Comprehensive Guidance According to Your Needs. Get in touch with us now!
Welcome Contact Us!
Henan Herm Machinery Co., Ltd
Email: info@hermmachinery.com
Whatsapp: 0086 18037508651